Handling Delicate Materials - Fine Cardiac Catheter Wires
Donald P. Labriola PE, President, QuickSilver Controls, Inc.
Special care needs to be taken when handling delicate materials used in medical applications. Small diameters provide increased flexibility needed for the long flex life applications, such as cardiac catheter wires. Many other applications also use these fine materials as winding and braiding materials: The medical device industry, microelectronics and composites. These materials are extremely fine - with sizes of wire less than 0.001” (25 micron), monofilaments of sizes down to 0.0005" (12.5 micron), multi filament fibers of 5 denier (5 grams per 9000 meters) and glass fiber optics of less than 0.004" (100 micron). These materials are unspooled from various size and styles of customer supplied packages and respooled onto the bobbins that the customer will use to manufacture their product. All while keeping the force between 5 and 10 grams (.05 - 0.1 Newton or 0.17 - 0.35 oz) for the case of .002" (50 micron) copper wires, with lower tensions used for other applications.
These force limits include the effects of dancer arm unbalanced weight (adjustable) as well as the dancer arm acceleration. Multiple loops to the dancer arm are used both to increase the force available to move the dancer arm and to increase the length of the material in the queue. The increased queue size allows for lower acceleration rates of the spools at startup and shutdown, as well as lower dancer arm acceleration for the same linear material motion. The reduction in force variation on the wire due to dancer arm acceleration is a product of these effects. A example system of 5 pulleys with the resulting 10 wire strands results in a reduction of acceleration based forces by a factor of 100 (10x for lower acceleration, 10x for the 10 loops almost perpendicular to the arm), while reducing the weight based forces by a factory of 10 compared to the typical single pulley configuration (with two wires - one on each side of the pulley, but typically further from perpendicular). A balance adjustment is used to set the nominal wire force. The number of pulleys used and be varied according to the desired force range.
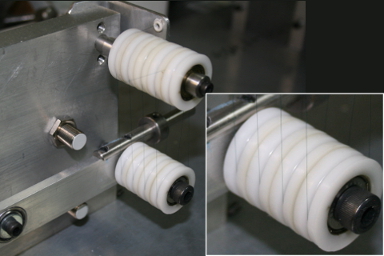
Figure 1 - Dancer Arm
A unique issue in handling these very fine wires is locating a robust position sensor that does not add any forces to a very light dancer arm. An optical range sensor with a sensing distance 5 to 40 cm provides position feedback. The optical range sensor relies on the target being diffusive (non-shiny) to provide a good reading. The raw output of these sensors is significantly not linear; an internal calculation in the SilverDust™ controller is used to linearize the feedback to simplify the control.
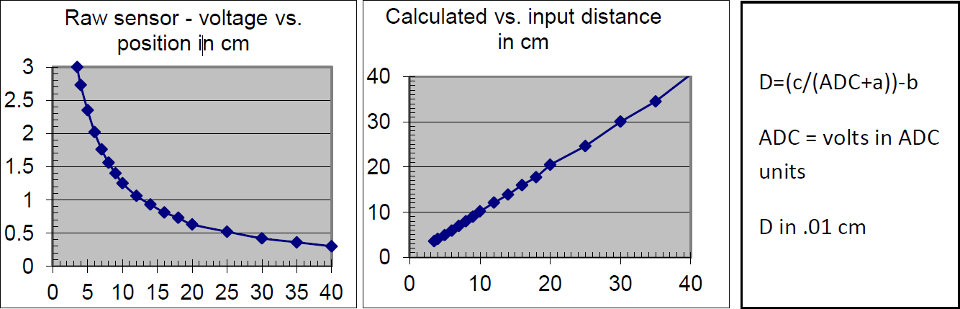
Figure 2 - Dancer Arm Linearization
The dancer arm motion is minimized by using the encoder signals from a traction spool feeding wire to the take up spooler and combining it with the dancer arm position. Internal calculations effectively determine and track the output spool diameter as the material builds up. The effective gearing ratio is reduces as the spool fills. The majority of the motion is then handled by this feed-forward gearing. The slight movements of the dancer arm resulting in slight adjustments to the feed-forward calculations, the motion of the dancer arm is also used to stabilize the system. The result is a dancer arm that slowly rises to the nominal position and then makes only minimal motions while in operation. Essentially a "dancer-less" arm!
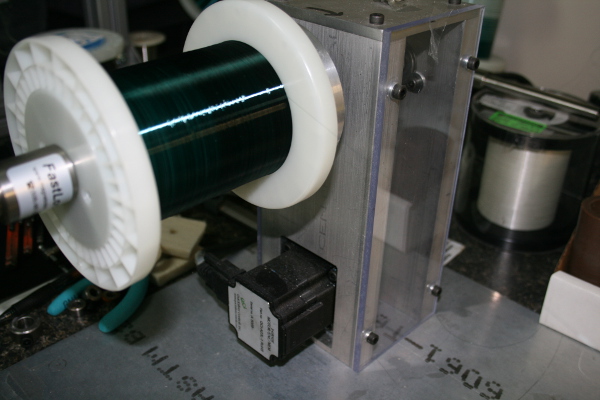
Figure 3 - Material on user supplied reels
Steeger USA in Inman, South Carolina, implemented this system using SilverDust™ controllers by QuickSilver Controls, Inc., San Dimas, California.
For more information: www.QuickSilverControls.com and www.SteegerUSA.com