Tuning, AutoTuning, and Damping – Optimizing What?
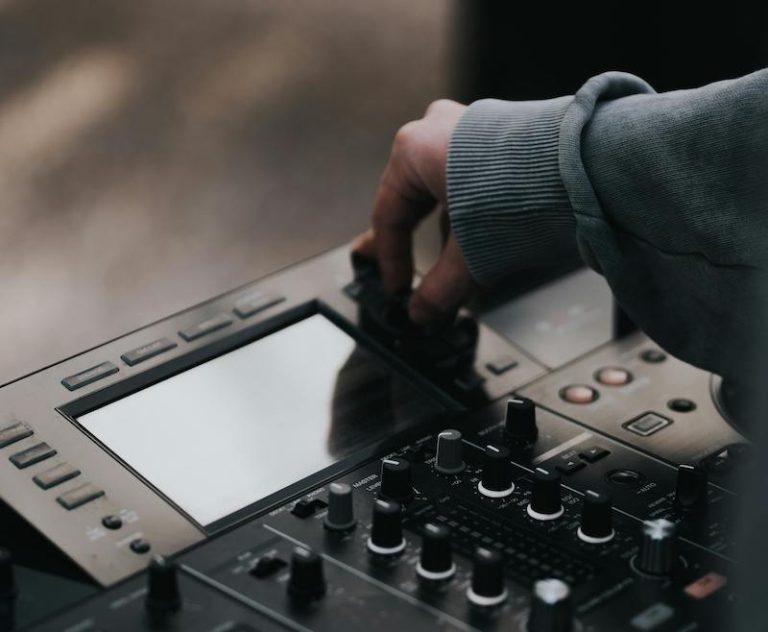
Interesting Projects Blog
June 13 2024 | Donald P. Labriola PE
Various servo controllers include “self-optimizing” tuning. Exactly what they are optimizing may not be the same as what the end user wants to optimize. Changing the tuning problem to make tuning easy and robust allows the user to control what “optimum” means for a particular application.
Fluid Handling requires tuning to minimize jerk in the mechanisms that are moving the liquid to keep the liquid inside the various probes moving it. A rapid downward motion with a sudden stop will cause the crane to stop, but the liquid may keep going. Intentional overdamping to match the time constant of the hydraulic circuit to the damping recovery of the motion can help optimize the motion time while keeping the sample intact. Pumping liquids requires a high gain margin to overcome stiction effects between a cylinder and the seals to keep the motion smooth, and often overdamping to keep the liquid from cavitating for small, precise delivery below liquid surfaces. When dispensing above the surface, then a rapid deceleration IS desired to cause the liquid to cavitate and split the stream to cleanly eject the liquid being delivered.
Animatronics requires higher damping, as well as speed dependent damping to effectively imitate human motions. Setting gains up until typical gain margins and phase margins make the motions very jerky and the high frequency components of the resulting motion can cause soft plastic and cloth portions of the character to oscillate unnaturally. Extremely quiet operation is also required.
Material handling has a wide range of differing needs. Powders adhere to the system limited by acceleration and jerk. There is a difference in profiling according to whether the intention is to disperse the materials or to prevent dispersion, or to try to move them in what resembles a fluid. Moving containers of fluid for dispensing – especially low viscosity materials with surfactants (such as diluted soaps) – requires a careful balance between speed of motion and prevention of bubble formation. Picking the correct motion timings and ramps as well as the degree of overdamping will speed the motion while also minimizing the residual wave in the bottle after the motion while preventing splashing which leads to bubbles.
Automated soldering of flexible circuits to substrates – think the little flex circuits in ink jet printers, for example – require rapid motion for throughput with close registration and then no motion while the solder is cooling to prevent bad solder joints from forming.
Medical office applications require smooth and accurate motions as well as very quiet operations – both when moving and when stopped.
Wide variations in loads is another issue not easily addressed by auto tuning. Adding damping to higher frequency realms while simultaneously keeping a good bandwidth for the motion for fast, precise, and quiet motions typically relies on adding damping to the system – fixed notch filters do not cover the changing resonances, especially when gearing is minimized or eliminated.
Damping in the system is typically only provided by the differential term in a PID controlled system. Notch filters may be added to such a system to try to reduce the effects of resonances, but bandwidth of the notch filter and the depth of the filter are typically inversely related – a deep notch filter has a very narrow bandwidth so slight system changes – load changes, belt tension, wear-in of gearheads – may cause enough shift in the resonant frequency to miss the notch frequency. A more robust solution – that also makes tuning much easier and robust – is to add multiple forms of damping to the system.
A More Robust Control Scheme used by QuickSilver Controls makes use of what they call PVIA – Position Velocity Integral Acceleration. We also use a drive method that uses software to control the impedance the motor sees looking into the driver circuitry – to add a tunable damping to the system, while also reducing the acoustic noise generated by the system. The velocity terms have programmable filters which help roll off higher frequency resonances allowing higher velocity gains to handle large inertia mismatches or to allow intentional overdamping as well as to attenuate noise generated by the incremental nature of an encoder feedback. The independent feedback and feed forward gains allow adjusting of the response to allow overdamping when desired, and to avoid overshoot when necessary. The acceleration term is filtered to simulate a viscous inertial damper. Up to two dampers can be configured. While notch filters typically try to drop the gain over a narrow frequency range to avoid resonances, Viscous inertial dampers add a significant amount of phase boost over a couple of octaves of frequency range. The added phase margin allows significant increase in allowable gain, reducing tracking error, allowing wide inertial mismatching and changes in loading, and helping with overcoming stiction. The system allows torque limiting and velocity limiting without the bandwidth limiting use of cascading stages, allowing for wide bandwidth and rapid motions.
QuickSilver systems ship with a nice compromise tuning that covers approximately 95% of our customers out of the box, covering approximately no inertia to 5x motor inertia, with the tuning adjustable through our QuickControl interface which includes heuristic tuning starting points for different loads. All of the other terms are integrated by the integrator, and a smart anti-wind up is incorporated which makes the tuning terms easy to adjust with minimal interaction.
The figures below show an approximately 100:1 inertial mismatch, and rapid motions for light loads, with a 40ms full revolution move and an 8ms 22.5 degree motion. Error is shown on the right axis.
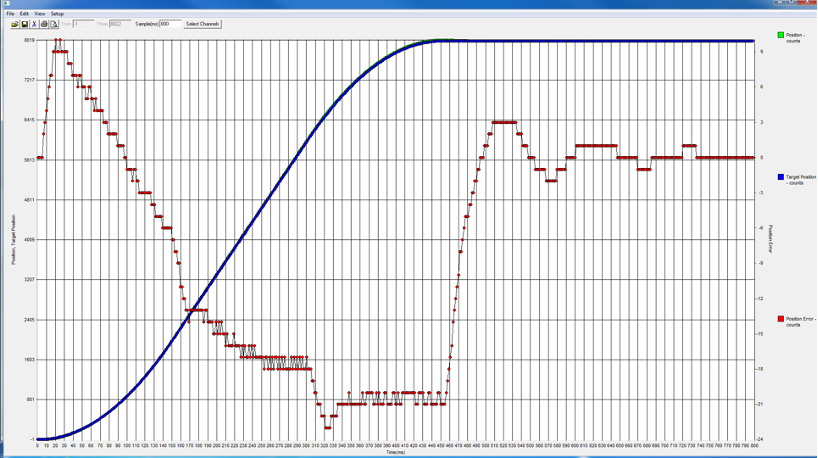
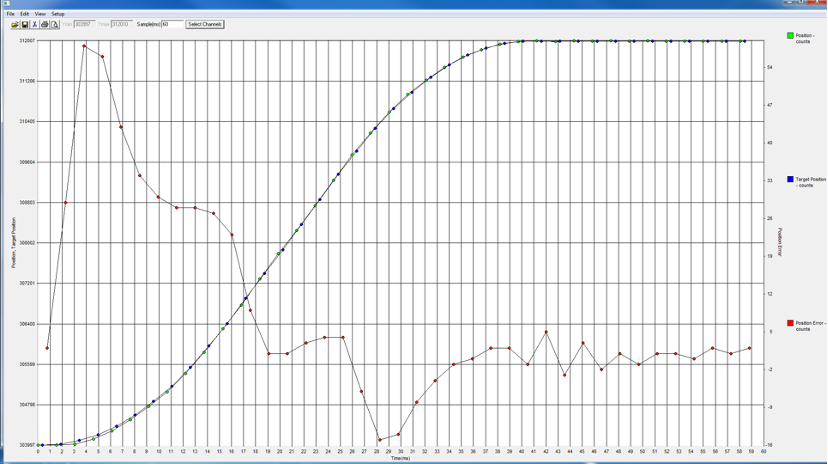
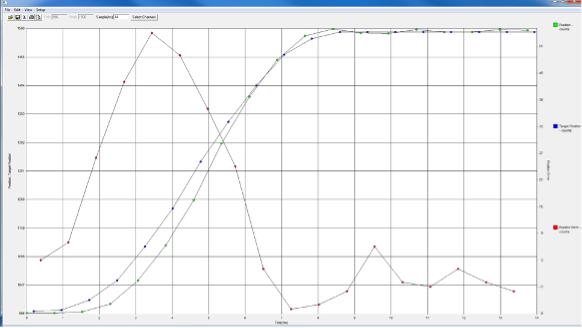
Related Posts
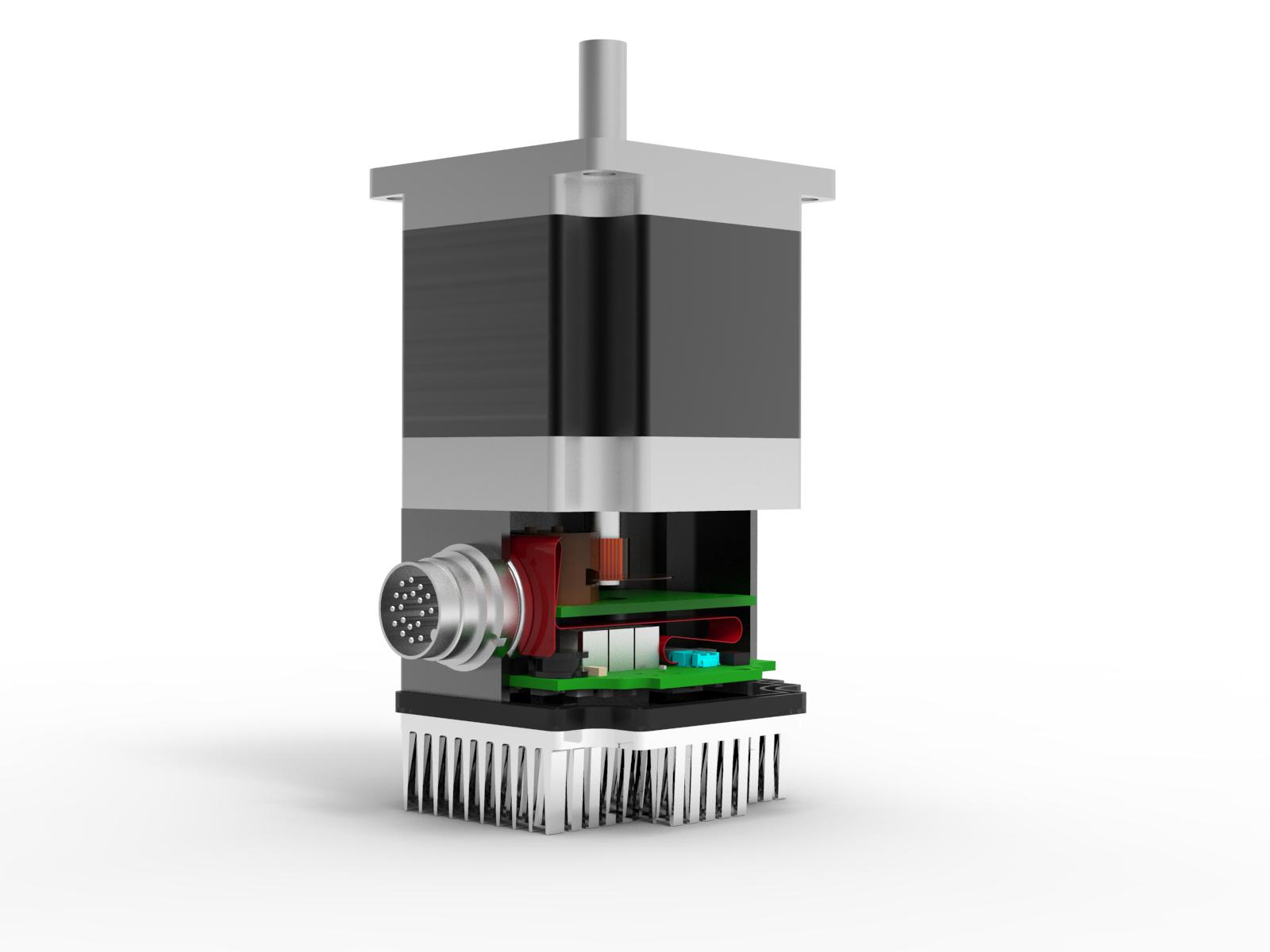
Operational Advantages of Integrated Motors
Operational Advantages of Integrated Motors Interesting Projects Blog April 17 2024 | Donald P. Labriola PE Combining a motor with
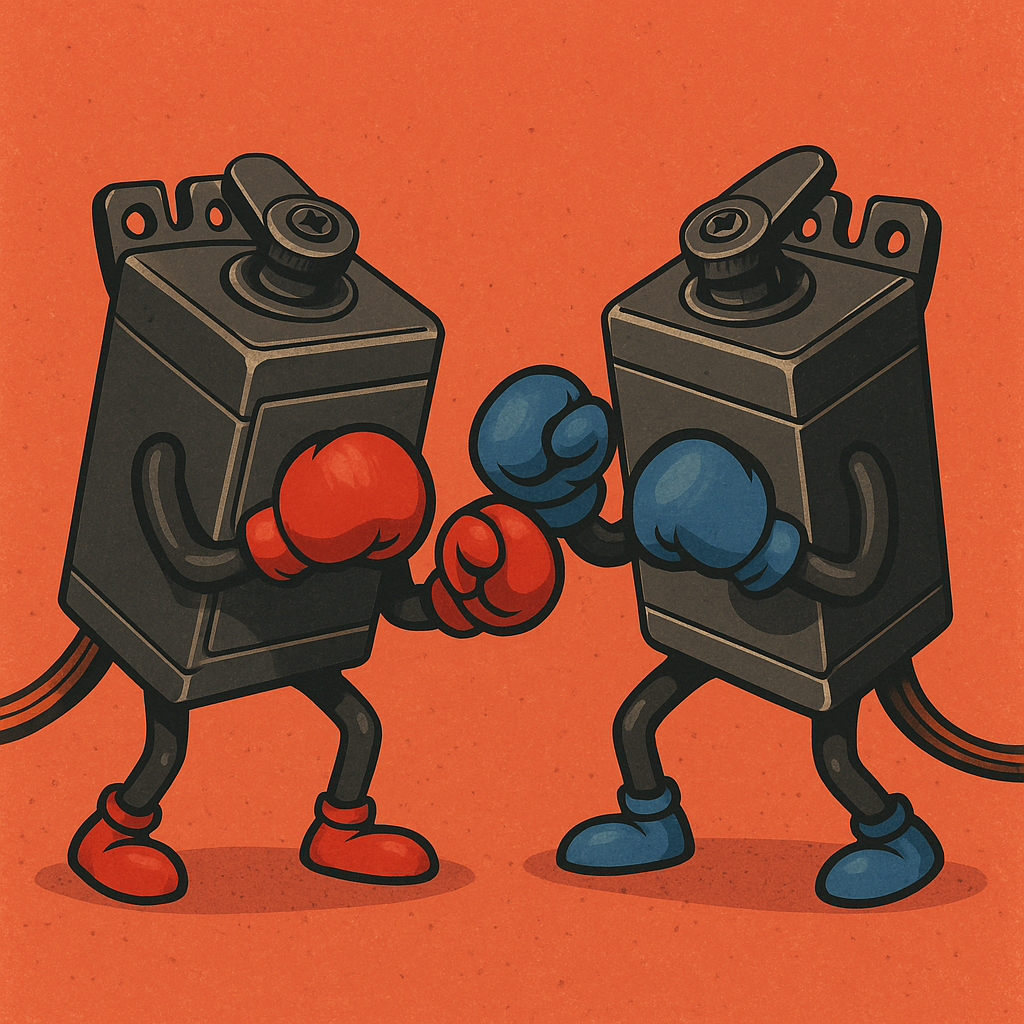
Integrated Hybrid Servo Motors Vs Standard Integrated Servo Motors
Integrated Hybrid Servo Motors Vs Standard Integrated Servo Motors Interesting Projects Blog April 10 2025 | Donald P. Labriola PE