The Hybrid Servo Motor – Stepping up to Closed Loop
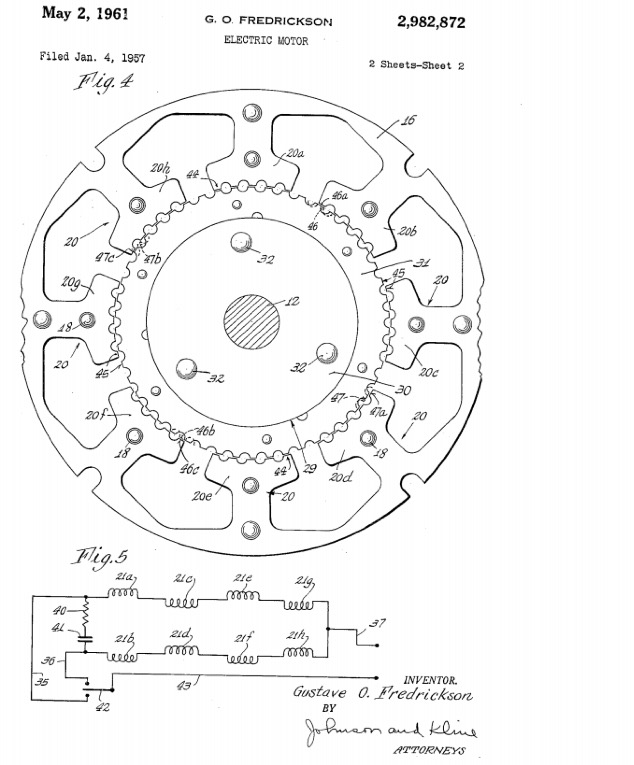
Interesting Projects Blog
October 1 2024 | Donald P. Labriola PE
Sophisticated control techniques have produced the Hybrid Servo Motor system from the motor style commonly called a Hybrid Stepper Motor when powered by an open loop step driver. The result is a high torque capability with a speed – torque range well matched to direct driving belts and lead screws, as well as other loads. Advanced control and damping enhancing techniques allow the out-of-the-box tuning to handle approximately 95% of the applications, covering open shaft to approximately 3-5x inertial mismatch without retuning the drive. With some additional tuning typically taking a few minutes, a 100:1 inertial mismatch is readily achieved. An example system consisting of a direct drive belt linear actuator, operated with 24 frame hybrid servo, was able to operate from no load to 11 kg (25 pounds) with no changes in tuning or motion. This corresponds to an inertial mismatch ranging from approximately 1:1 to 22:1, again without retuning.
A Short History of the Hybrid Motor
The high pole count, Hybrid Transverse motor has now gone full circle. The term Hybrid in the name refers to the generation of torque both by variable reluctance and by reaction with permanent magnets. Transverse refers to the three dimensional nature of this motor, with the magnet field polarized axially.
This motor goes back, under various names to at least 1957 – US patent 2,982,872. It originated as a 2 phase motor so it could be driven as split phase synchronous motor from a single phase AC line: one phase tied directly to a 60Hz line, and the other phase shifted by the use of a series RC circuit. For smoothness this early patent describes 48-50 stator-to-laminate tooth spacing ratio. Later in its history, this unique motor was operated in step mode (US 3,343,014), using overlapping pulses to replace the original sine and cosine waveforms. The rotor-stator tooth ratio of 50:50 was used to enhance accuracy when operating full step. Eventually, half-stepping, and increasing levels of microstepping resolution were created. The motor stator-rotor tooth ratio was returned to a prime ratio of either 48:50 or 52:50, to implement better microstepping. The driving waveforms have improved to the point that they now do good approximations of the original sine waves used to this motor style. Finally, closed loop control has been added to control this high-pole synchronous motor as a true brushless servo motor – the Hybrid Servo.
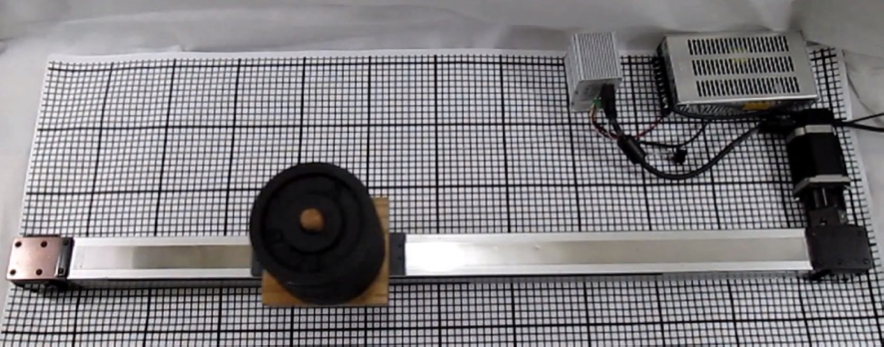
The Drive Determines the Operation: Open Loop = Stepper
This unique motor has benefits of high continuous torque and low manufacturing cost, but the actual performance and operation of these motors, as with others, are strongly dependent upon the attached drive.
Just as with a 3 phase motor, the attached electronics determine the operation. When operated with a typical stepper drive, the current is controlled, commonly with either peak current sensing or hysteric mode. If the driving voltage is sufficiently higher than the back-EMF of the motor, the current tends to follow the commanded current and is fairly independent of the motor motion. As the current is not significantly modified by the motion (particularly at lower speeds), the pure current mode drive provides little interaction and thus only light damping. Low damping results in strong low speed resonances (with their attendant torque drop outs) and long settling time at the end of motion.
A typical 1.8 degree motor has 100 magnetic poles which results in 50 electrical cycles per revolution. The motor, when energized with a constant drive current, produces a sinusoidally varying torque as it is rotated. Different phase current combinations offset the null point rotation angle. The use of a high pole count both increases the peak torque value and reduces the mechanical angle needed to traverse from maximum positive torque to maximum negative torque. The resulting steep torque versus position characteristics (torque stiffness) which results is part of what makes this style of motor motor good for open loop positioning , as even a small error angle results in a significant change in torque which opposed the torque producing the error.
The figure compares motors varying only by pole count, a 100 pole motor and an 8 pole motor. The magnetic gearing produces approximately 100/8 = 12.5 times as much torque, and the period is 12.5 times smaller, so the slope of the torque versus position curve is some 150 times as steep.
The strong torque versus error angle characteristic of this motor also gives rise to resonance problems seen when these motors are operated open loop. The motor rotor inertia acting against the sinusoidal correcting torque forms a rotary pendulum. For small angles one may consider this as a k-Theta rotary spring coupled to the second moment of inertia of the rotor assembly. The resulting interaction causes a resonance, which reduces the available torque near the resonance frequency, can make the motor run roughly, lose position, or even stop running all together. This same resonance sets the ringing characteristics when the motion stops. Note that the spring constant is a function of torque constant times the excitation current. Varying the current changes the effective spring constant, and thus the resonant frequency. This effect can be used intentionally to try to avoid the resonance, or can happen accidently with driver tolerances or temperature changes, causing some mechanisms to operate properly while others fail.
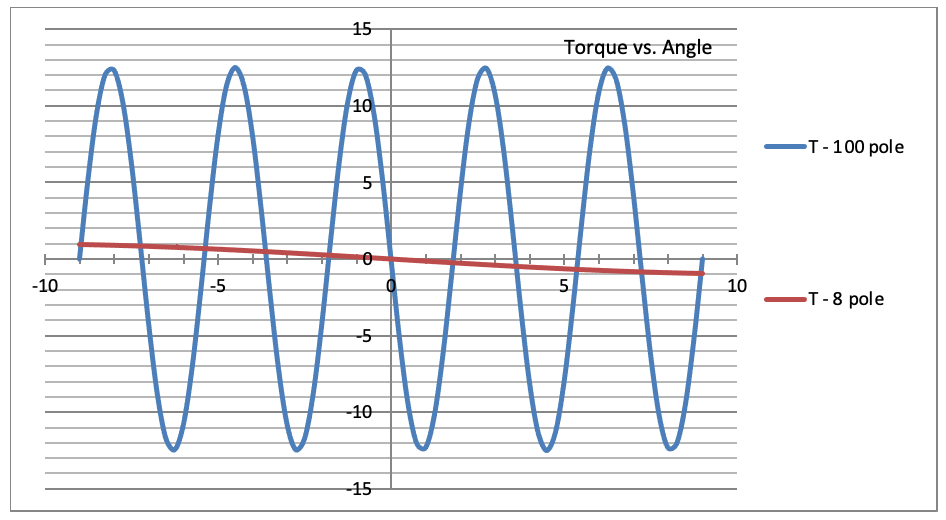
System Damping
Damping in the system reduces the amplitude of the resonance, affecting both the running torque dip and the ringing when stopping. This can be introduced by both mechanical and electronic means. Viscous inertial dampers couple a flywheel to the rotor shaft via the viscous oil. Changing the motor shaft speed causes shearing of the oil between the damper housing and the fly wheel, causing the flywheel to slowly (relative term) match the shaft (damper housing) speed. For those periods when the flywheel and the shaft have different speeds, heat is being dissipated by the oil. An oscillation in the system causes a periodic variation in shaft speed. With a properly chosen damper – one having an adequate inertia and proper oil viscosity to set the desired frequency band for operation – a significant portion of the oscillation may be damped out. These dampers are very effective, but they take up space
and add weight, add inertia to the system which must be accelerated by the motor. Quality units are also relatively costly. The cost may be reduced by using frictional magnet dampers, but their performance is not as good as the viscous dampers, and they may introduce dust (metal particles).
Electronic damping may be produced by varying the current as a function of velocity. Early examples of this used an extra set of coils on the motor to act as a velocity sensor. The signal from this sensor was used to modify the requested current waveform. With the velocity sensor signals acting as a proxy for the back-EMF of the motor, this effectively reduces the driver impedance from very high with a pure current drive to significantly lower, which allows for dissipation of the rotary vibration into the driver circuitry. The low impedance of the driving voltage source with a line connected synchronous motor helps dampen these motors, as an excess of speed generates power into the line, while a lagging position draws additional power. This effect of driving with a low impedance can be easily seen by shorting the leads of the step motor and trying to turn the shaft!
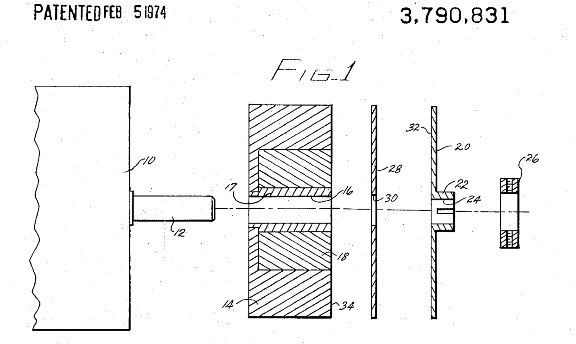
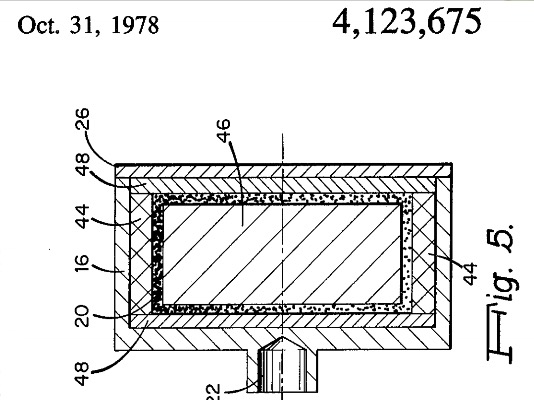
Closed Loop: Commutation
Step loss avoidance is used in some “closed-loop” products – the quotes here indicate that there is not general agreement whether or not step loss avoidance should be called closed loop. Rather than commutating the motor based on motor position, the motor normally follows an open loop trajectory generator motor angle. When the motor position error reaches approximately +/- 90 electrical degrees (one full step) from the commanded position, the angle from the trajectory generator is constrained to follow what the motor is able to do rather than the originally commanded trajectory; only in these instances is step loss avoidance acting as commutation. Step loss avoidance prevents the loss of steps, but it does not actually eliminate the motor resonances. It also does not maximize motor efficiency, resulting in hotter motors. While it does eliminate the need for tuning, the flip side is that it has no provision for damping nor tuning, and does it does not generally allow for torque control.
Brushless commutation varies the phase of the winding excitation as a function of motor position. For a position control systems, this generally requires some type of rotor position feedback. Commutation applies sine and cosine current waveforms (or truncated versions of these) to the motor windings based on rotor position and commanded torque. These currents waveforms may be modified to handle field weakening at higher speeds, and may also be modified to compensate for motor torque ripple as well as cogging torque.
Low Frequency Resonance Elimination
The use of sinusoidal commutation with this motor minimizes the variation of torque as a function of rotor position (given the commanded torque is held constant). Assuming the ideal of constant torque, the k-theta “spring” has been replaced by a constant force “spring”. The pendulum no longer has a restoring force, so it does not oscillate. This eliminates the low frequency resonance by reducing a 2nd order oscillatory system to a first order system. With the resonance eliminated, the torque no longer drops out and the motor operates more smoothly.
Hybrid Servo
The hybrid servo is the evolution of the hybrid transverse motor for service as a brushless servo. The hybrid servo varies from a traditional low pole count brusheless AC servo by: 1) number of poles, 2) by the use of 2 phases versus 3 phases, and 3) peak to continuous torque. Ideally, both are sinusoidally commutated using a position sensor (for positioning operation). The higher pole count of the hybrid servo trades speed for torque. In comparing the two motor types, given the magnetic gap strength is maintained, the speed goes down linearly with the number of poles and the torque goes up by the same factor. This is commonly referred to as “Magnetic Gearing”. Various papers have shown that the torque density and losses of a 2 and 3 phase motor of similar design are identical – there is not an advantage either way. In the early days of brushless motors, a 3 phase motor had the advantage of two less power switches, but as the cost of the electronics drops, this is no longer significant.
The low pole count motors typically are designed with a larger air gap which allows higher current densities before saturating the magnetic structure. The larger gap also requires more magnetic material to generate a given gap magnetic field strength, adding to cost. The net result is that these motor types may have roughly equivalent maximum low speed torque capability, but the low pole count version can typically only maintain this peak torque for a few seconds due to heating from the high currents (up to 10x continuous current rating produces 100x resistive heating!). The high pole count versions operated at nominal current can maintain a similar torque level on a continuous basis.
Control System Features
The control system determines the requested torque based on actual and measured position, as well as velocity and acceleration. The velocity and acceleration (when used) are typically derived (estimated) from the position, although higher performance system may supplement with separate sensors.
In addition to the conventional control terms, additional damping methods may be added to the system. The QuickSilver Controls, Inc. methodology adds both active and a passive damping. The active damping algorithm is a real-time simulation of the effects of a viscous inertial damper on the system. This is able to significantly boost the phase margin of the system over a couple of octaves of bandwidth. The extra phase margin enables higher tuning gains while still minimizing overshoot.
The synthetic (simulated) viscous damper does not provide the full phase boost available from the mechanical version, due to resolution, bandwidth limitation, and processing delay. However the simulated damper does significantly improve system performance at no incremental cost, no added weight or volume, and no added system inertia. It does not wear out, and it is easily adjusted.
Driver Impedance Control
Passive damping is implemented as an algorithm which varies the driver output impedance as a function of frequency. Lower frequency operations emulates current mode, while higher frequencies are handled as voltage mode. This produces good torque control in the frequency range used to control normal motions, while significantly damping higher frequency energy associated with motor shaft torsional resonances. This again allows for higher gains for tighter controls while still having good damping and stability.
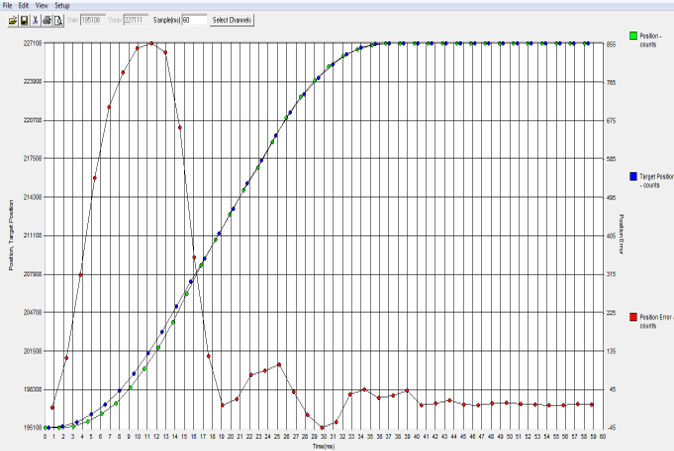
Summary
Hybrid servos are now becoming more popular as their control techniques are understood, and as sufficient processing power is becoming inexpensive. The highly tooled nature of the hybrid transverse motors, combined with the reduced magnet material requirements, make for cost effective systems. New advances in low cost and high resolution position feedback, utilizing magnetic, capacitive sensing, and new methods such as the Mosolver which adds small sense coils on a flex circuit within the stator to determine position, are continuing to drive cost down and performance up. The high continuous torque capability and a power curve which matches well into many systems without the need for a gear head, further reducing costs and improving reliability. Although they still look like a “Stepper Motor”, the performance of the Hybrid Servo has distinctly superior performance!
Related Posts
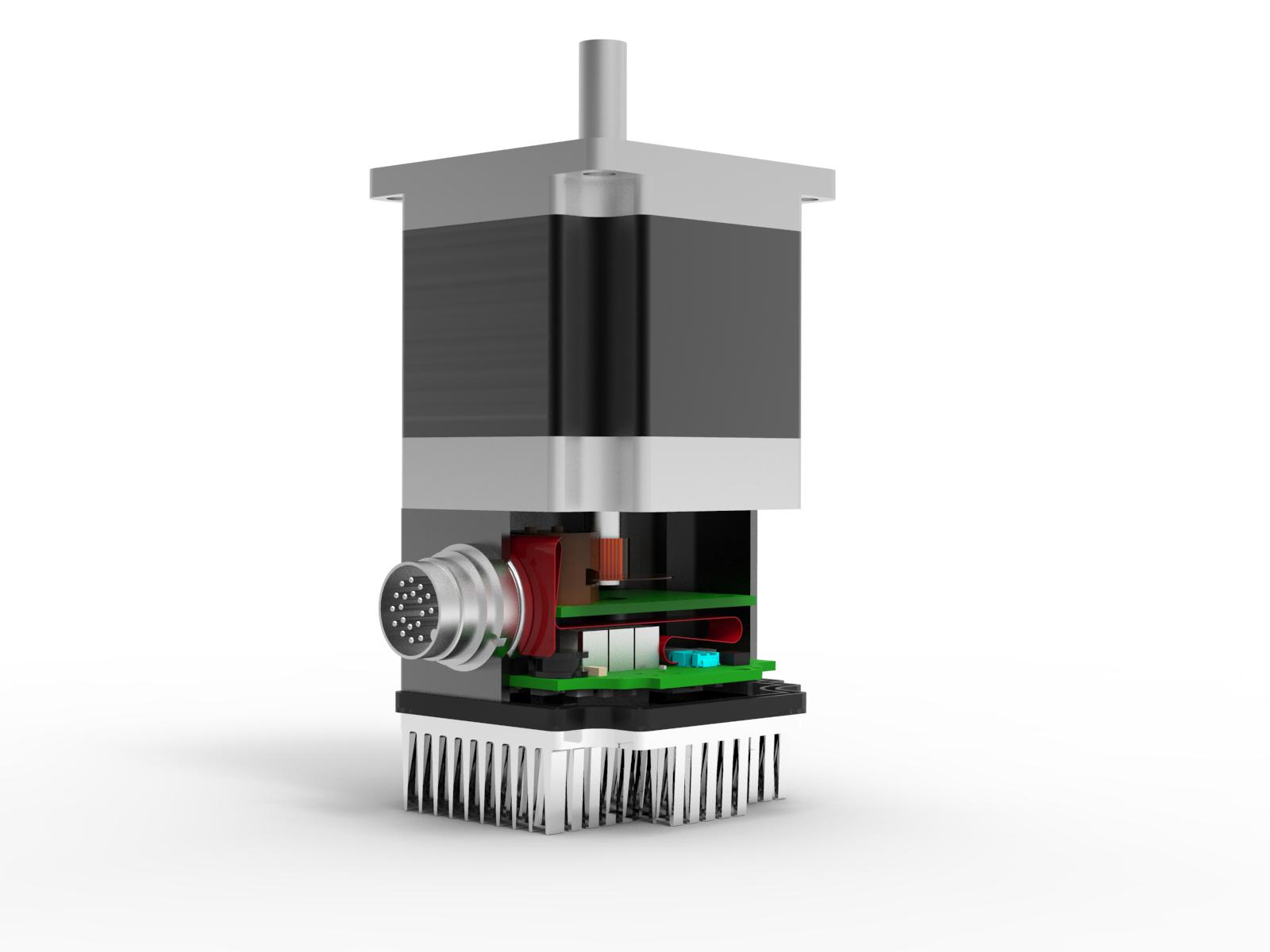
Operational Advantages of Integrated Motors
Operational Advantages of Integrated Motors Interesting Projects Blog April 17 2024 | Donald P. Labriola PE Combining a motor with
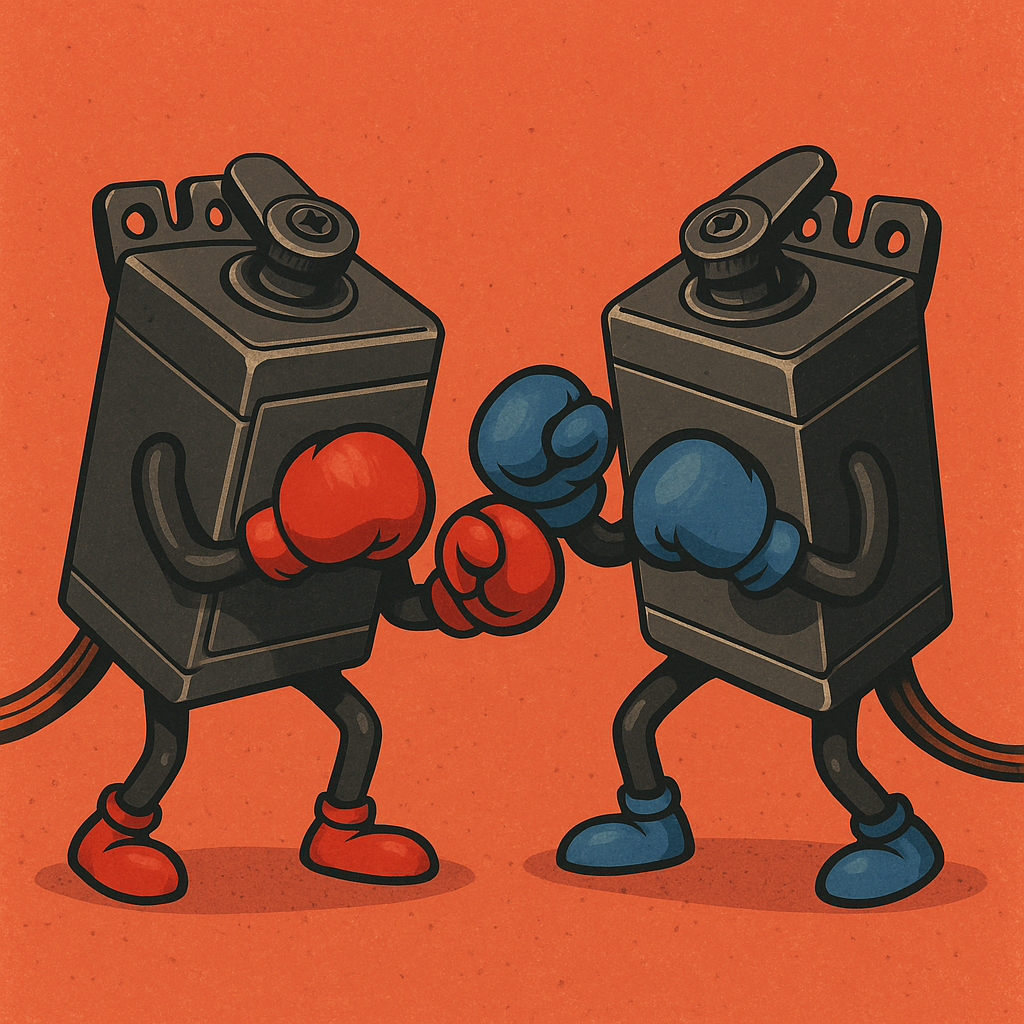
Integrated Hybrid Servo Motors Vs Standard Integrated Servo Motors
Integrated Hybrid Servo Motors Vs Standard Integrated Servo Motors Interesting Projects Blog April 10 2025 | Donald P. Labriola PE
Great article!
Very detailed article, it helped me a lot, thank you